The world is changing, is your organisation ready?
Our global network of experts offers their insights into the challenges facing business today.
You may also be interested in
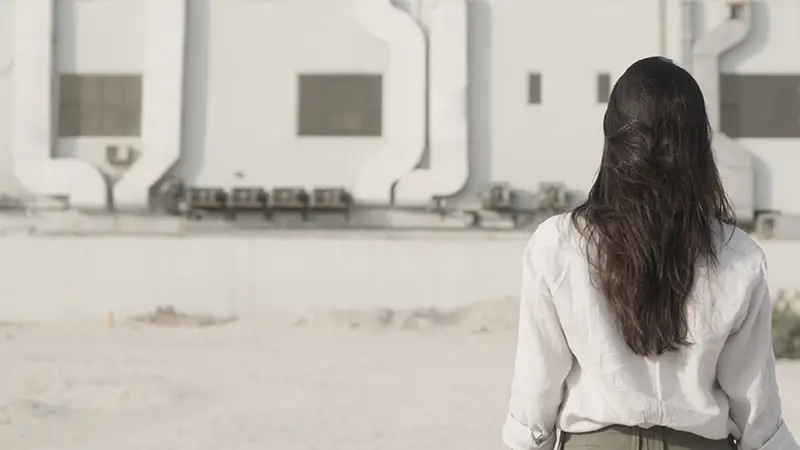
Client Stories
Stories from our work with clients.
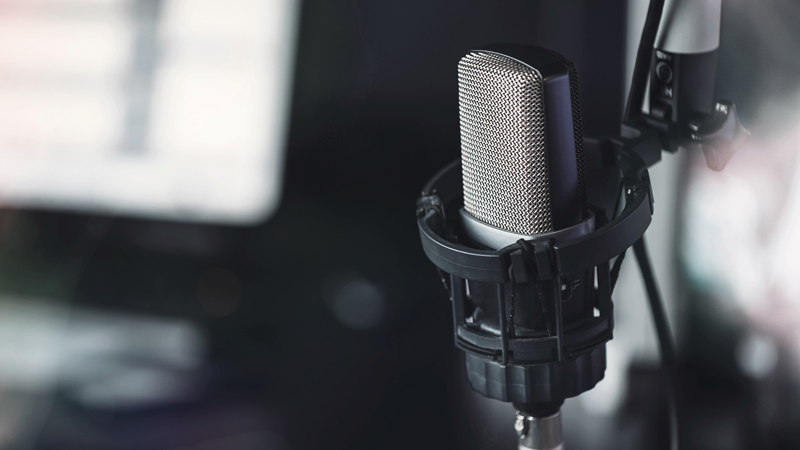
Control Risks Podcast
Podcasts from Control Risks featuring expert analysis and discussion of the most pressing global and regional issues.
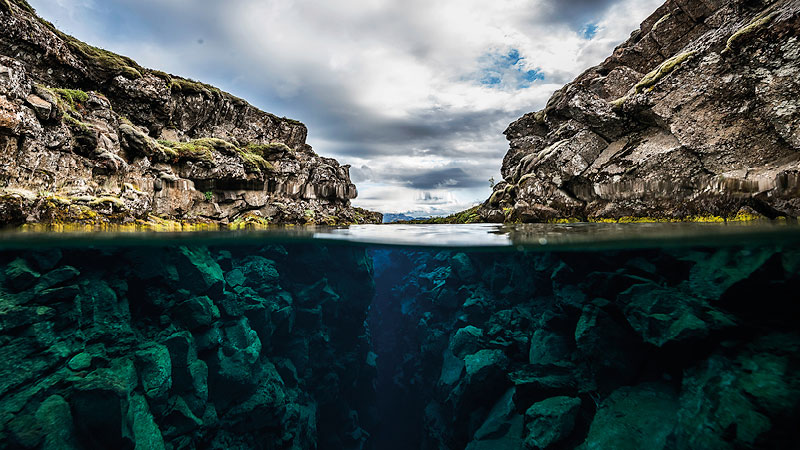
Global Monthly Briefing
Receive our analysis and insights straight to your inbox every month
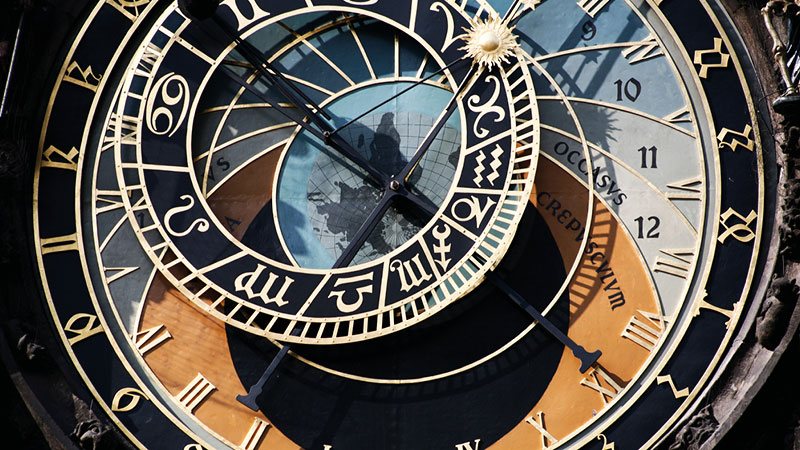
Geopolitical Calendar
Geopolitical Calendar: The essential guide to events that will shape the coming year